1. Introduction
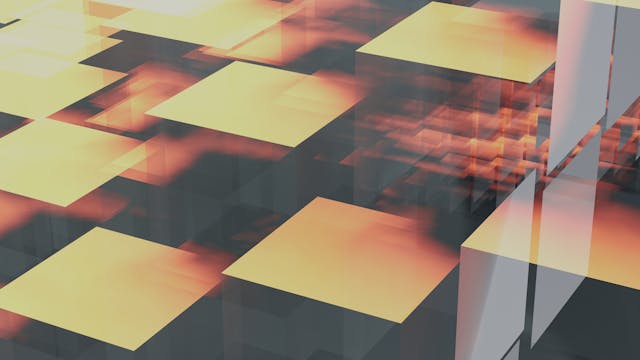
Due to a lack of workers, numerous sectors around the world have experienced serious difficulties recently. Businesses are having trouble filling positions with enough workers to handle the demands of their operations, whether they are in manufacturing, agriculture, healthcare, or the hospitality industry. These shortages may result in lower output, higher expenses, and occasionally, the inability to successfully meet client needs.
One possible way to alleviate these labor shortages in various industries is through robotics. Through the integration of automation and artificial intelligence technology, tasks that would often require human intervention can now be performed by robots. This change not only makes it easier to overcome the difficulties caused by a lack of human resources, but it also makes a variety of processes more accurate, efficient, and scalable.
Robotics has the ability to completely transform businesses by enhancing the capacities of human workers, covering gaps in the labor market, and increasing overall operational efficiency. Embracing robotics offers a chance to streamline procedures, boost output, and guarantee company continuity despite shifting labor conditions as companies continue to manage the challenges of labor availability.
2. Current Labor Shortages
Many sectors of the economy are currently experiencing severe labor shortages. The industries most impacted include manufacturing, hospitality, healthcare, and technology. For these sectors to meet demand and guarantee efficient operations, qualified labor is vital.
A number of variables play a part in the scarcity of skilled labor in these vital industries. One significant factor is the aging workforce, since many seasoned workers are retiring and creating a void that is difficult to fill with younger talent. The market has shifted in favor of jobs requiring more specialized training or education, which has further reduced the number of eligible applicants.
The labor deficit has been made worse by shifting societal norms and demography. Fewer people are joining the workforce to replace those who are retiring as birth rates fall and populations age in many countries. There is pressure on sectors that need highly qualified labor or specialized knowledge due to this demographic shift.
Rapid technological development has led to the creation of new employment roles requiring specific technical abilities, which has had an impact on labor shortages as well. The need for workers with digital proficiency is increasing as automation and artificial intelligence become more common in numerous industries, which is expanding the skills gap in traditional fields like manufacturing and healthcare.
As I mentioned earlier, combating labor shortages calls for a multipronged strategy that takes into account both short-term requirements and long-term fixes. Industries need to adjust by investing in training programs to create a pool of qualified workers, upskilling current employees, and investigating cutting-edge technologies like robotics to automate labor and relieve the burden on human resources. Businesses can better manage labor shortages and maintain their viability in a changing market by utilizing technology and embracing change.
3. Role of Robotics in Addressing Labor Shortages
Because robotics technology can supplement human work in a variety of industries, it is essential in alleviating labor shortages. Robots can carry out physically demanding and repetitive tasks with accuracy and efficiency, which eliminates the need for a lot of human labor in these kinds of jobs. Businesses can increase productivity, maintain constant quality standards, and lessen the workload on employees by automating these processes.
Robots have been effectively used in industry to boost output, optimize production processes, and lessen the need for manual labor. Robotic arms are used by automakers to weld, paint, and assemble auto parts at speeds and accuracy that are significantly faster than those of humans. This reduces the possibility of human error in these crucial processes and guarantees consistency in the quality of the final product.
Agriculture is another sector that benefits from robotics; in this sector, robots are utilized for planting, watering, harvesting, and sorting produce. These robots help farmers overcome human constraints during busy seasons or when there is a lack of accessible workforce by working nonstop for hours on end without experiencing weariness or pauses. Despite manpower shortages, businesses in agriculture may meet demand and retain efficiency by implementing robotics.
Robotics has been adopted by the healthcare industry to improve patient care and help medical personnel with a variety of activities. Surgical robots facilitate more accurate surgeries with less intrusion, speeding up patients' recuperation and increasing their results. Additionally, robots assist caretakers by helping with patient rehabilitation exercises or moving large objects, relieving the physical strain that comes with being overburdened in the healthcare industry.
Robotics technology is still proving its worth in a variety of industries by efficiently replacing human labor in situations where there are constraints or shortages. Its capacity to complete monotonous jobs quickly, precisely, and nonstop presents a long-term way to close the labor gap while fostering creativity and productivity at work.
4. Advantages of Implementing Robotics
There are several benefits to robotics implementation across sectors. One of the main advantages is the significant improvement in productivity that results from robots' ability to operate nonstop around the clock, which eventually raises output levels. Using robotics in operations improves productivity by minimizing human error and simplifying procedures, which results in a more efficient workflow and reliable results.
The enhancement in product quality attained through robotic accuracy is a noteworthy benefit. Robots produce goods that regularly satisfy high standards because they are precise and repeatable in their task execution. In the end, this saves time and money by decreasing waste and rework in addition to meeting client expectations.
Over time, robotics solutions may prove to be more cost-effective than traditional labor in terms of labor costs. Robotic system setup has upfront expenditures, however over time, these costs are frequently offset by higher productivity and lower operating costs. Because they can do jobs more quickly than people, robots help firms maximize profits by producing more in less time.
5. Challenges and Considerations
There are many obstacles to take into account while introducing robotics into the workforce. The initial high cost of integrating robots technology is one of the main challenges. Businesses must spend money on buying the robots, preparing staff to operate with them, and maintaining the machinery. Not all tasks lend themselves to automation, particularly those that call for intricate decision-making or human intervention.
Replacing human workers with robots raises ethical and social implications. One major worry with automation is that it could result in job displacement for people whose jobs are replaced by machines. This may exacerbate economic instability and income inequality in areas where certain industries play a significant role. Treating employees who are being replaced fairly and facilitating their move to other opportunities present ethical challenges.
Robotics integration into labor-short industries requires striking a balance between ethical obligations and technological advances. Businesses need to carefully evaluate the effects on their employees and communities, taking into account initiatives for job redistribution, retraining, and open communication regarding automation plans. Businesses, legislators, and labor leaders must work together to effectively solve these issues and advance a sustainable future for technological advancements as well as workers.
6. Case Studies: Successful Implementation of Robotics
Robotics has been effectively applied in a number of industries to overcome the manpower shortage. Robots are used by automakers like Tesla and BMW to do assembly, painting, and welding duties. These robots replace human labor in repetitive and potentially dangerous jobs by increasing efficiency and maintaining high precision levels.
Robotic systems are being used by warehousing and logistics corporations such as Amazon to perform jobs such as packing, sorting, and picking. In order to reduce labor costs, increase accuracy, and satisfy the expanding needs of e-commerce, these robots collaborate with human workers.
By giving surgeons more accuracy and agility during operations, robotic helpers like the da Vinci Surgical System have transformed surgical techniques in the medical field. By speeding up patients' recuperation, these developments also assist hospitals in filling the manpower gap in specialty medicine.
These case studies show how robotics may augment human workforces, boost productivity, and uphold consistent quality standards to effectively mitigate labor shortages across a range of industries.
7. Future Outlook: The Evolution of Robotics in Workforce
Future Outlook: The Evolution of Robotics in Workforce
It's clear that robotics will become more and more important in determining how work is done in the future. Forecasts indicate that robotics will keep changing industries by increasing production, precision, and efficiency. We predict a sharp increase in the use of robotic automation in a variety of industries, including customer service, manufacturing, healthcare, and logistics.
The merging of robots and artificial intelligence (AI) to usher in a new era of intelligent automation is one significant development to keep an eye on. It is anticipated that this combination will allow robots to carry out increasingly complicated activities on their own, adjust to shifting surroundings, and make choices based on data analysis done in real time. Robots' skills will be further enhanced by developments in sensor technology and machine learning algorithms, which will make them more adaptable and flexible in their operations.
The emergence of collaborative robots, sometimes known as cobots, is another fascinating trend in the works. These robots are made to coexist peacefully with people, sharing workspace and tasks without the need for security or fences. We may anticipate increasing human-robot collaboration in a variety of contexts as cobots grow more advanced and more reasonably priced, fostering safer and more productive working conditions.
Small and medium-sized businesses will probably adopt automation solutions as robots technology becomes more widely available and reasonably priced in order to maintain their competitiveness in the market. By democratizing access to cutting-edge technology that were previously only available to major organizations, this democratization of robots will level the playing field for companies of all sizes.
To sum up everything I mentioned above, robotics in the workforce has a very bright future ahead of it. Robotics will revolutionize our way of working through ongoing innovation and integration with AI technology, opening up new avenues for productivity increases and economic expansion. Organizations hoping to prosper in an increasingly automated world—where human ingenuity mixed with robotic accuracy yields previously unheard-of levels of productivity and success—will need to embrace this transition head-on.
8. Training and Upskilling for a Robotic Workforce
Employees collaborating with robots must participate in training and upskilling programs in order to adjust to changing job demands. The workforce's adoption of robotics emphasizes how critical it is to equip workers with the know-how to successfully operate and cooperate with automation technologies. Businesses may enable their employees to use robotic technologies effectively and ensure a seamless transition while mitigating the effects of labor shortages by providing thorough training. Employee development investments strengthen performance and job satisfaction while future-proofing careers in an increasingly automated workplace by promoting a culture of continual learning.
9. Regulatory Environment: Ensuring Ethical Use
It is critical to take into account how laws and regulations can guarantee the ethical application of robotics while discussing the legal landscape surrounding them in the workplace. With the development of technology, there is an increasing demand for precise regulations that control how robots are integrated into different businesses while upholding moral principles and human rights.😜
In order to safeguard employees from physical injury, current regulations frequently concentrate on safety procedures and technological requirements for robotic systems. But as robots become more autonomous and capable of making decisions for themselves, more laws covering more ethical issues must be passed.
Key problems that need consideration in legislative frameworks are data privacy, algorithmic bias, employment displacement, and accountability in the event of errors or accidents. Maintaining ethical standards in the employment of robotics in the workplace requires procedures for oversight and restitution as well as transparency in the decision-making processes of the robots. Policymakers, business leaders, ethicists, and other interested parties must work together to create comprehensive policies that strike a balance between innovation and morality.
10. Collaboration between Humans and Robots
Cobots, or collaborative robotics, are a revolutionary approach to manufacturing that allow humans and robots to operate side by side in a shared workspace. These cutting-edge robotic systems are made to work alongside human laborers on jobs that call for strength, speed, endurance, or precision that is beyond the capabilities of a human. Cobots can function securely in close proximity to people thanks to sensors and programming that sense their presence and immediately slow down or stop their motions.
In addition to addressing the labor crisis, the idea of human-robot collaboration increases production and efficiency across a range of industries. Cobots optimize workflows by utilizing the skills of both humans and robots. This allows human workers to concentrate on more complicated decision-making processes or activities requiring creativity and emotional intelligence, while machines do repetitive or dangerous duties. The combination of robotic automation and human experience produces better output quality, fewer errors, and more production capacity overall.
In the workplace, collaborative robotics promotes a culture of ongoing learning and adaptability. By interacting closely with robotic systems, human workers can gain practical experience in programming, operating, and maintaining these technologies. In addition to improving job happiness, upskilling gives workers useful technical skills that are becoming more and more important in the current digital economy. Collaborative robotics is really about equipping workers with new skills and tools for the workplace of the future, rather than just displacing labor.
11. Conclusion
Based on the aforementioned, it can be inferred that robotics offers a revolutionary approach to addressing the problems caused by a lack of workers in many sectors. Robots can ease the burden of a labor shortage while increasing production and efficiency by automating repetitive jobs and supplementing human workers. Incorporating robots technology not only bridges current labor shortages but also creates opportunities for more innovation and expansion in the workforce. Businesses that continue to use robotics solutions are changing the nature of work to make it more competitive and sustainable over time, not taking the place of people. In spite of persistent labor issues, adopting this technological breakthrough can result in a workforce that is more resilient and a vibrant economy.
12. Call to Action
It is critical to look at creative ways to address these issues as the effects of labor shortages across industries become more apparent. One particularly promising approach to effectively addressing and overcoming labor shortages is robotics. Businesses may increase efficiency and optimize operations by leveraging automation and cutting-edge technologies.👌
For this reason, I implore businesses to learn more about robots and think about making an investment in robotic solutions. Adopting automation improves productivity, accuracy, and cost-effectiveness across a range of activities in addition to mitigating the effects of labor shortages. It's time to give implementing these cutting-edge technology top priority if you want to help your company achieve long-term success and growth.
Let's take this chance to embrace robotics and completely transform how we address the labor problem. Adopting automation will open doors for improved operational efficiency and competitive advantage in addition to filling the vacuum left by the lack of skilled labor. To stay ahead in today's changing business environment, it is necessary for companies to give investigating and incorporating robotic solutions into their operations top priority.
I urge all parties involved to acknowledge the potential of robotics to mitigate the scarcity of labor and propel advancements across all industries. By making investments in robotic technology, we can strengthen our industries' resilience and adaptability for the future while also addressing today's problems. Together, let's go out on this revolutionary path towards a robotics-driven future that is more sustainable and productive.