1. Introduction:
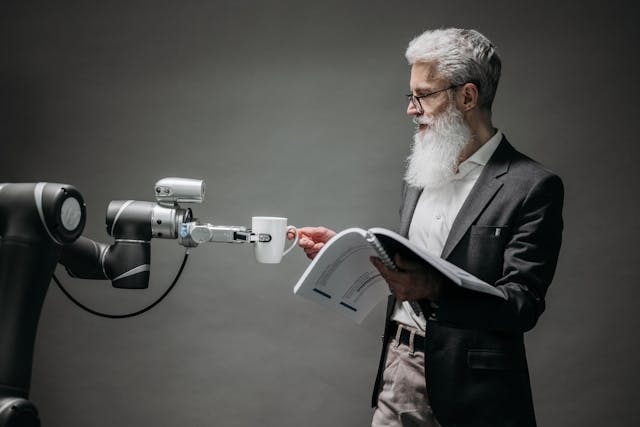
With previously unheard-of levels of connectivity and data interchange, the Internet of Things (IoT) is transforming conventional methods in the field of metal manufacturing. With the use of networked devices, this technology may gather and evaluate data to enhance productivity, efficiency, and decision-making in metal fabrication processes. In order to improve quality control, cut lead times, boost overall competitiveness, and quickly respond to shifting market needs, organizations are placing a greater emphasis on agility. Adopting IoT solutions is a calculated risk for metal fabrication businesses trying to maintain competitiveness in today's changing market and optimize operations.
2. Traditional Challenges in Metal Fabrication:
Agility and efficiency have been hampered in traditional metal production by issues like machine downtime, manual monitoring, and wasteful procedures. Production schedules can be affected and delays might result from machine downtime brought on by malfunctions or maintenance problems. The quality and consistency of manufactured metal parts are impacted by the labor-intensive and human error-prone nature of manual machine and process monitoring. Relying on antiquated workflows and technologies can make it more difficult to quickly adjust to shifting business expectations. These difficulties show that metal fabrication operations require a more automated and streamlined approach.
In the metal fabrication industry, machine downtime is a major worry because it not only impacts production timelines but also raises operating expenses. In fabrication factories, machinery frequently operates nonstop, thus any unscheduled downtime can lead to lost income and productivity. The manual monitoring of machinery introduces an additional level of complication, as it necessitates continuous supervision by staff members who might not always identify problems immediately. The laborious, time-consuming, and error-prone nature of this manual procedure may have an adverse effect on the finished metal goods' quality.
Conventional methods for fabricating metal might be inflexible and unable to adapt to changing consumer needs. The inability to quickly switch to new product lines or grow production is a result of outdated procedures. Effective resolution of these difficulties can be achieved by integrating IoT technologies into metal fabricating operations. Real-time machine and process monitoring, predictive maintenance to minimize downtime, and data-driven insights to maximize workflow efficiency are all made possible by the Internet of Things. Metal manufacture is revolutionized by using IoT solutions since they increase productivity, decrease costs, and improve agility.
3. IoT Applications in Metal Fabrication:
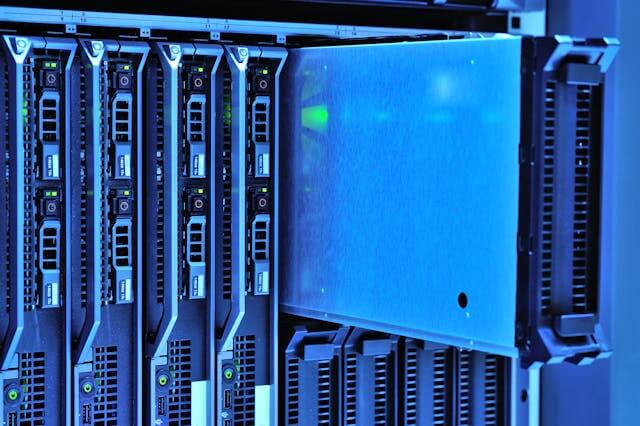
IoT applications are transforming the metal production sector by using sensors to track machine performance and anticipate maintenance requirements. These Internet of Things (IoT) sensors collect data in real time on a range of parameters, including vibration, temperature, and power usage. Manufacturers can proactively detect any problems before they develop into expensive downtime or equipment failures by keeping an eye on these variables. The overall operational efficiency and machine uptime are maximized with the use of this predictive maintenance strategy.
In metal fabrication operations, real-time analytics are essential for production optimization and quality monitoring. When IoT technology is integrated into the production line, firms may instantly gather enormous volumes of data. Then, in order to find any irregularities or departures from quality requirements, this data is examined in real-time. Operators can guarantee constant product quality and conformity to specifications by seeing problems early and taking prompt corrective action.
By providing real-time monitoring and analysis of critical performance parameters, the integration of IoT applications in metal manufacturing not only increases operational agility but also productivity, lowers maintenance costs, and improves product quality.
4. Enhanced Connectivity and Data Analysis:
The Internet of Things (IoT) is transforming metal manufacturing by making processes more nimble than ever before. Enhanced connectivity and data analysis are key components of this revolution. Real-time monitoring and control over the manufacturing line are made possible by interconnected devices, which provide smooth communication and coordination between machines. This increased connectivity allows for predictive maintenance based on sensor data, which reduces downtime while also improving workflow efficiency.
By providing insightful analysis of the massive amounts of data created by connected devices, big data analytics further enhances the potential of the Internet of Things in the metal fabrication industry. Manufacturers can enhance productivity and quality by identifying trends, streamlining processes, and making well-informed decisions through the analysis of this data. Making proactive decisions and promoting continuous improvement in metal fabrication processes is made possible for decision-makers by the capacity to predict equipment breakdowns or spot chances for process optimization through data analysis.
Essentially, big data analytics and improved connectivity through networked devices are revolutionizing the metal fabrication industry by boosting productivity, agility, and competitiveness in a quickly changing business environment.
5. Adaptive Automation with IoT:
The Internet of Things (IoT) is enabling adaptive automation in metal manufacturing, which is transforming precision machining procedures. The Internet of Things makes it easier to put adaptive control systems into place, which can modify machining parameters in real time in response to ongoing input from sensors included into machines. Higher quality results are produced as a result of this dynamic responsiveness's ability to improve metal fabricating operations' accuracy and efficiency.
IoT gives real-time insights into manufacturing processes, which allows for dynamic scheduling in the metal fabrication industry. Manufacturers may collect data on machine performance, material utilization, and workflow efficiency by embedding IoT devices across the manufacturing floor. Agile decision-making about production schedules is made possible by this data, allowing for prompt modifications to accommodate unforeseen delays or shifting demand.
Essentially, the metal fabrication industries are increasing their productivity and agility through the use of IoT technology for adaptive automation, which eventually improves operational efficiency and customer satisfaction.
6. IoT-driven Supply Chain Management:
The metal fabrication business has undergone a revolution thanks to the incorporation of IoT into supply chain management. Manufacturers may precisely monitor inventory levels, expedite order processing, and improve logistical operations by utilizing IoT technology. IoT devices' real-time data insights enable more accurate inventory tracking, preventing overstockpiling and guaranteeing that goods are always available when needed.
The notable decrease in lead times is one of the main advantages of IoT-driven supply chain management in the metal fabrication industry. Manufacturers are able to proactively solve any potential delays or faults in the production process because to the real-time monitoring and predictive maintenance capabilities provided by IoT sensors. This proactive strategy guarantees a smoother flow of operations and minimizes downtime, which eventually results in shorter lead times and faster production cycles.
Manufacturers may fortify their supplier connections by integrating IoT technology into supply chain management. Manufacturers and suppliers can work together more successfully to adjust delivery dates and satisfy demand changes by exchanging real-time data on inventory levels and production schedules. All stakeholders engaged in the supply chain benefit from improved communication and confidence that is fostered by this greater transparency, which strengthens supplier relationships and streamlines procurement procedures overall.
To sum up, the integration of IoT technology in supply chain management is revolutionizing the metal fabrication sector by improving operational effectiveness, cutting lead times, and cultivating closer ties with suppliers. In today's fast-paced market, manufacturers who adopt IoT-driven solutions stand to gain enhanced agility, optimized operations, and a competitive advantage.🎚
7. Promoting Worker Safety and Well-being:
Wearable IoT devices have become indispensable tools for monitoring worker health and safety on the job; they can track vital signs, detect potential hazards like high temperatures or dangerous gases, and even alert workers in real-time to prevent accidents before they happen. This is just one of the many ways that IoT is revolutionizing metal fabrication.
The implementation of IoT-powered predictive maintenance is also significantly contributing to the creation of a safer work environment in metal manufacturing facilities. Through the use of sensors and data analytics, predictive maintenance is able to continuously monitor equipment and identify possible problems before they arise. This proactive strategy ensures a more secure and stable operation overall by preventing unplanned malfunctions that could threaten employees and interrupt workflow.
8. Case Studies: Successful Integration of IoT in Metal Fabrication:
Case Studies: Successful Integration of IoT in Metal Fabrication
Company X is a prominent manufacturer that has integrated IoT sensors into its assembly processes, providing an excellent example of IoT integration in metal fabrication. Within the first six months of implementation, Company X considerably increased their productivity by 20% through the collection of real-time data on equipment performance and production efficiency. Reduced downtime and improved operational procedures have resulted from the capacity to remotely monitor equipment and anticipate maintenance requirements.
Company Y is a small metal fabrication workshop that has successfully incorporated IoT-powered quality control technologies into their operations. Through the use of sensors to track temperature, pressure, and alignment during welding and cutting processes, Company Y was able to minimize material waste by an impressive 15% because of greater accuracy and fewer errors. This improvement resulted in lower expenses as well as an overall improvement in the quality of their manufactured goods, which raised consumer satisfaction levels.
A medium-sized metal fabrication company called Company Z used cloud-based smart inventory management systems as a means of utilizing IoT technology. They were able to automate reordering when supplies ran low, expedite the procurement process, and track raw material levels in real time thanks to this solution. As a result, Company Z saw a significant 25% decrease in the cost of keeping goods on hand and a reduction in stockouts, which improved overall operating efficiency and allowed for more flexible production schedules.
These case studies show how IoT adoption in the metal fabrication industry can lead to observable advantages like higher productivity, cost savings through waste reduction, or better inventory management techniques, which ultimately result in higher-quality goods and services for both consumers and businesses.
9. Overcoming Security Challenges with IoMT (Internet of Metals Things):
The Internet of Things (IoT) is transforming efficiency and processes in the field of metal manufacturing. But there are drawbacks to this progress, particularly with regard to cybersecurity threats posed by interconnected gadgets. These worries take on greater significance with the emergence of the Internet of Metals Things (IoMT). Ensuring the integrity and security of information in metal production activities requires careful consideration of data transmission and storage protocols.
Strong cybersecurity measures must be put in place in order to address security issues related to IoMT in metal fabrication. In order to secure data transmission between linked devices, encryption is essential. Encryption greatly lowers the possibility of unlawful interception or tampering during communication processes by encoding information into a format that only authorized parties can access.
Adopting secure networks and protocols is essential to preserving data integrity in the Internet of Medical Things ecosystem. An additional line of defense against online attacks is provided by the use of secure communication protocols like HTTPS or the implementation of virtual private networks (VPNs). By establishing safe routes for data sharing, these solutions lessen the possibility of security lapses or cyberattacks on networked metal fabricating equipment.
Regular audits and upgrades are essential best practices for improving cybersecurity in IoMT applications, in addition to encryption and secure networks. System activity monitoring, vulnerability detection, and quick security patch application all reduce the risks brought on by changing cyberthreats. Businesses engaged in metal production should strengthen their defenses against malicious actions targeting connected devices by being proactive and vigilant in addressing any security weaknesses.
In order to control user permissions and prevent unwanted access to sensitive data within the IoMT architecture, access control measures must be established. In the context of metal fabrication, implementing robust authentication methods like multifactor authentication guarantees that only authorized users can communicate with networked devices or systems. Organizations can stop unauthorized people from jeopardizing vital data integrity or system functions by adopting stringent access controls.
Integrating Internet of Things (IoT) technologies, such as IoMT, into metal production processes requires careful consideration of data transmission and storage security. In the digital era of manufacturing, firms can improve their cybersecurity posture and efficiently manage possible hazards associated with connected equipment by implementing encryption techniques, secure networks, frequent audits, and access controls. Setting cybersecurity as a top priority not only safeguards sensitive data but also fortifies overall operational resilience in the increasingly interconnected world of innovative metal manufacturing.
10. Future Implications and Innovations in Agile Metal Fabrication:
Future Implications and Innovations in Agile Metal Fabrication:
Future developments like blockchain traceability and AI integration have the potential to completely change the metal fabricating industry. Algorithms based on artificial intelligence (AI) can improve overall productivity in metal fabricating facilities by forecasting maintenance requirements and streamlining procedures. Manufacturers may make data-driven decisions that increase productivity and decrease downtime by utilizing AI-powered analytics.
Throughout the supply chain, the incorporation of blockchain technology provides unmatched transparency and traceability. Stakeholders can use blockchain to safely follow the path of raw materials, confirm authenticity, and guarantee adherence to industry norms. In the event of quality problems or recalls, this facilitates quicker problem-solving in addition to building trust.
Projecting how agile manufacturing processes will develop in the future as a result of ongoing IoT breakthroughs shows that operations will become even more efficient due to networked gadgets. Real-time machinery performance monitoring, predictive maintenance based on machine data analysis, and improved component-to-component communication within a manufacturing environment are all made possible by the Internet of Things (IoT).
Metal production operations can attain previously unheard-of levels of agility and responsiveness by utilizing IoT technologies. Production lines with built-in communication between machines will be able to adjust to changes in demand or material availability and self-optimize. For metal products, this dynamic environment will mean lower costs, more flexibility, and a quicker time to market.
After putting all of this together, we can say that there is a lot of promise for metal fabrication processes to be revolutionized by the confluence of blockchain, AI, and IoT technologies. Manufacturers who adopt these advances will have an advantage over their competitors in a market that is changing quickly. Agile metal production will become a crucial differentiator for innovators and a mainstream practice as we transition to a more connected and data-driven future. 📚
11. Sustainability Impact of IoT-enabled Metal Fabrication:
IoT's influence on metal fabrication extends to sustainability since it promotes efficient processes that reduce waste production. IoT systems improve efficiency by enabling real-time monitoring and predictive maintenance, which lowers the possibility of mistakes or overproduction in metalworking processes. As a result, less material is wasted, which eventually helps to make fabrication more environmentally friendly.
An important factor in improving energy efficiency in metal fabrication processes is IoT technology. Manufacturers can pinpoint areas for improvement and put energy-saving measures into place by gathering and evaluating data on machine performance and resource usage. By reducing excessive energy consumption, this not only lowers the environmental impact of metalworking operations but also saves money.
IoT technology integration in metal fabrication improves operational agility and promotes waste reduction, energy efficiency, and ultimately a more environmentally friendly production process, all of which have a good effect on sustainability. 😌
12. Conclusion:
The Internet of Things (IoT) has improved agility in a number of ways, which has drastically changed the metal production industry. Real-time equipment and process monitoring is made possible by the use of IoT devices and sensors, which boosts productivity and efficiency. IoT systems' data-driven insights improve quality control, streamline processes, and reduce downtime in metal manufacturing operations.
To gain a competitive advantage in the metal fabrication business, industry participants must embrace digital transformation via IoT technology. Businesses that include IoT technologies can increase productivity, cut expenses, and provide better products with quicker delivery times. Those who do not adjust run the danger of lagging behind rivals who use IoT to spur efficiency and innovation in metal manufacturing processes.
Investing in IoT skills is now not only attractive but also essential for sustainable growth and success in this ever changing market. Metal fabrication companies may stay ahead of the curve, better satisfy client requests, and ultimately prosper in a market that is becoming more and more competitive by utilizing the power of IoT.