1. Introduction: Setting the Scene
Building a successful factory of the future is essential to being competitive and satisfying the expectations of tomorrow's markets in today's quickly changing industrial landscape. Conventional manufacturing processes have been completely transformed by the incorporation of cutting-edge technology like automation, Internet of Things (IoT), and artificial intelligence. For manufacturers to effectively traverse these changes, they must proactively adapt and modify their operations. This blog post examines six essential measures that can help companies create a forward-thinking factory that values efficiency and creativity.
In order to embrace digital transformation, the first phase involves incorporating smart technology into the production processes, such as sensors and Internet of Things devices. Through the use of real-time data analytics, firms can increase overall operational performance, forecast maintenance requirements, and optimize production efficiency. Investing in automation technologies to reduce human error and streamline repetitive operations is the second step toward increasing productivity. In addition to increasing productivity, automation frees up staff members to concentrate on more strategic duties that call for human interaction.
The third step emphasizes how important it is to use cobots, or collaborative robotics, in a manufacturing environment. These robots assist human workers on the manufacturing floor, improving flexibility, efficiency, and safety. Adopting machine learning-powered predictive maintenance techniques is the focus of the fourth step. By anticipating possible equipment problems before they happen, predictive maintenance helps save expensive downtime by allowing proactive maintenance as opposed to reactive repairs.
The significance of upskilling the workforce to guarantee they have the abilities needed to function well in a digitally driven world is emphasized in the fifth stage. Retraining initiatives and ongoing training programs can facilitate employees' seamless transition to new procedures and technologies. Step six, the last one, emphasizes how important it is to develop an innovative culture inside the company. The factory can maintain its technological leadership and drive continual progress by fostering experimentation, idea sharing, and cross-departmental collaboration.
Companies may create a solid basis for constructing an agile, effective, and sustainable factory of the future in an increasingly competitive market by adhering to these six crucial stages.
2. Step 1: Defining Goals and Objectives
Establishing precise goals and objectives is the first step towards creating a successful factory of the future. Because it determines the course of your transformation journey, this phase is very important. A clear understanding of your goals guarantees that all of your resources and efforts are directed toward the same goal.
Goals must be SMART (specific, measurable, attainable, relevant, and time-bound) in order to be effective. Well-defined objectives offer a clear picture of what must be done. Measurable objectives enable success and progress monitoring. Realistic and reachable objectives guarantee that they are within your means. Goals that are pertinent are in line with your overarching plan and vision. Time-bound objectives set clear deadlines for completion, which help your team stay accountable and engaged.
By setting SMART goals in the initial stages of building your factory of the future, you lay a strong foundation for successful implementation and growth.
3. Step 2: Embracing Technology
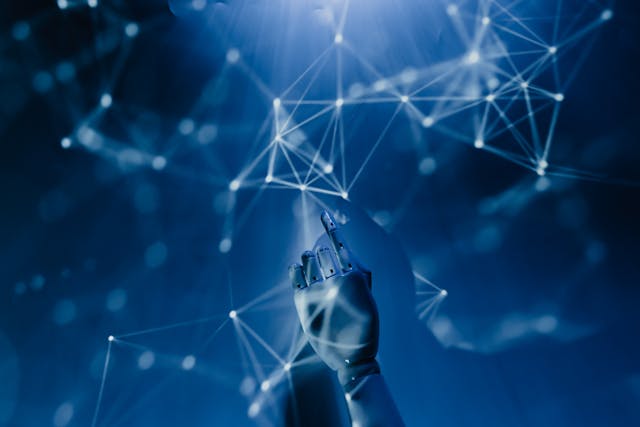
A crucial first step in creating a successful Factory of the Future is adopting technology. Thanks to its ability to increase production, flexibility, and efficiency, technology is a key component of modern industries. Traditional manufacturing processes are being revolutionized by major technologies such as automation, data analytics, artificial intelligence (AI), and the Internet of Things (IoT).
Factories can reduce manual errors and streamline operations by utilizing automation. Real-time data communication between machines is made possible by IoT, which enhances equipment efficacy and maintenance schedules. Predictive maintenance is one example of an AI application that may forecast machine breakdowns ahead of time and drastically minimize downtime. Factories can now use data analytics to make well-informed decisions by using insights from massive databases.
Advanced technologies, such as 3D printing, are revolutionizing the manufacturing industry by facilitating quick prototype and more affordable, customized production. Cobots, or collaborative robots, and robotics collaborate with human laborers to improve the efficiency and caliber of manufacturing. In order to teach staff and simulate production scenarios for ongoing improvement, augmented reality (AR) and virtual reality (VR) are used.
Using these cutting-edge technology not only makes operations more efficient, but it also opens doors for increased creativity and competitiveness in the quickly changing industrial environment. Factories may lead Industry 4.0 and achieve long-term success and sustainability in the digital age by strategically embracing technology.
4. Step 3: Data-Driven Decision Making
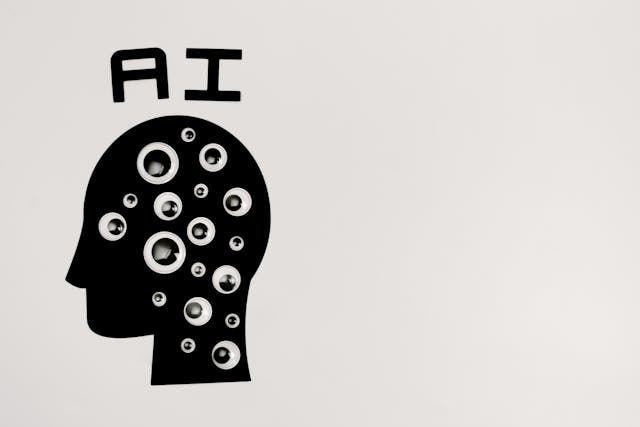
Step 3: Data-Driven Decision Making
Data is essential for streamlining processes and creating a profitable factory of the future. Factories can improve overall performance, cut costs, and increase efficiency by utilizing data-driven decision-making processes. Gathering pertinent information from multiple sources within the plant enables a thorough analysis that can result in well-informed judgments.
Effective data collection, analysis, and utilization in an industrial context can be achieved in a number of ways. Throughout the factory floor, IoT devices and sensors can be used to offer real-time data on production levels, ambient conditions, and equipment performance. For additional investigation, this data can be compiled and kept in centralized databases.
Advanced analytics techniques like predictive modeling and machine learning algorithms can be used to analyze this data and provide insightful analysis that can be used to find bottlenecks, forecast maintenance requirements, or improve production schedules. Decision-makers can quickly act upon this information when it is presented in a relevant manner through the use of visualization tools such as dashboards or reports.
In the age of smart manufacturing, factories may stay ahead of the competition by adopting data-driven decision-making techniques that enable them to foresee problems before they arise, adjust to changing market demands more effectively, and continuously improve operations.
5. Step 4: Building a Skilled Workforce
Building a competent workforce is the fourth step in creating a successful factory of the future. Employee upskilling has become essential since industrial landscapes are being shaped by rapid technological breakthroughs. In order to meet this need, businesses must fund training initiatives that give employees the know-how to effectively use automation and operate contemporary equipment.
Several tactics can be used to promote a culture of ongoing learning and development among employees. Ensuring that staff have access to online workshops, certificates, and courses on developing technology helps to keep them informed about changes in the sector. Providing opportunities for employees to expand their skill set through cross-training also helps them become more adaptable. Establishing mentorship programs that allow seasoned employees to advise recent hires promotes knowledge transfer and skill development across the whole company.
6. Step 5: Sustainable Practices and Green Initiatives
Achieving long-term success in Step 5 of creating a successful factory of the future requires incorporating green initiatives and sustainable practices. Adopting sustainability has several advantages for the company as a whole in addition to helping the environment by lowering waste and carbon footprint. Businesses that put sustainability first frequently save money by optimizing their resources, reducing waste, and using less energy. Engaging in such measures can improve a brand's reputation and draw both investors and eco-conscious customers.
Eco-friendly practices can be incorporated into factory operations in a number of ways. One strategy is to maximize energy use by making investments in renewable energy sources, such as wind turbines or solar panels. Energy consumption can be greatly decreased by putting energy-efficient practices and technology into place, such as smart heating and cooling systems, energy-efficient machinery, and LED lighting. Reducing the amount of trash produced by implementing circular economy ideas, recycling initiatives, and material reuse wherever feasible is another tactic.
This valuable resource can be preserved with the aid of sustainable water management techniques like rainwater collection or water recycling systems. Reducing the usage of single-use plastics and switching to compostable or biodegradable packaging materials can also help with environmental conservation efforts. A culture of environmental responsibility and innovation is fostered by involving employees in sustainability projects through training programs and creating green teams inside the firm. By implementing these tactics, manufacturers can lessen their long-term environmental impact while simultaneously increasing their competitiveness and operational effectiveness.
Building a successful factory of the future requires integrating sustainable practices into manufacturing operations. Businesses can help the environment and their profit line by putting sustainability first. Encouraging a culture of environmental responsibility among employees, reducing waste output, and optimizing energy usage are just a few ways to make factories more environmentally friendly without sacrificing their competitiveness in the market.
7. Step 6: Continuous Improvement and Adaptability
The sixth step in creating a successful factory of the future is all about adaptation and constant development. Being flexible and nimble is essential in today's fast-paced and constantly-evolving market to stay ahead of the curve. Consistently assessing performance measures, getting input from stakeholders, and making iterative adjustments in response to these discoveries are important strategies for accomplishing this.
The aims and objectives of your factory must be in line with the performance indicators you set in order to guarantee continual improvement. Frequent measurement and analysis of these indicators will reveal areas for improvement and offer insightful information about how well the current processes are working. Getting input from suppliers, consumers, and staff can provide a variety of viewpoints on how to improve operations.
The foundation of creating a factory that is prepared for the future is iterative improvement. Through the implementation of a continuous feedback, evaluation, and refinement cycle, firms can promptly address emerging challenges and adjust to dynamic market needs. Adopting a continuous improvement culture not only encourages creativity but also creates a dynamic atmosphere where teams are encouraged to work together to effect positive change.
It is critical to maintain flexibility and agility through continuous improvement methods in order to construct a prosperous factory of the future. Regular performance evaluations, obtaining input from a variety of sources, and iterative process improvement are ways that organizations can improve their overall competitiveness in the manufacturing industry, as well as their operational efficiency and ability to adapt to changing market conditions.
8. Conclusion: Looking Ahead to the Factory of Tomorrow
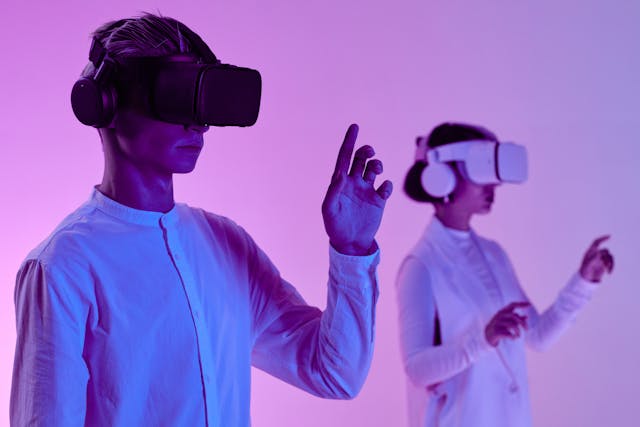
To sum up, creating a successful factory of the future requires a number of crucial stages. First of all, a purpose-driven organization is built on the foundation of clearly defined goals and objectives. Second, using cutting-edge technologies and automation boosts production and efficiency. Thirdly, putting sustainability first guarantees sustainability over the long run while adhering to environmental regulations.
Encouraging innovation in the workplace stimulates workforce creativity and adaptation. Enhancing skills and improving overall performance are supported by investing in staff training and development. Ultimately, in an industrial landscape that is constantly changing, the ability to remain flexible in response to shifting market demands is essential to long-term success.
We envision a factory of the future where artificial intelligence (AI), machine learning, and the Internet of Things (IoT) are further integrated to further automate processes and enable predictive maintenance. Applications of augmented reality (AR) and virtual reality (VR) have the potential to completely change training curricula and improve operational effectiveness.
The emergence of 5G-connected smart factories will enable real-time monitoring and decision-making for the optimization of manufacturing processes. Circular economy models, the use of renewable energy, and waste reduction programs are examples of sustainable practices that will eventually become standard operating procedures for manufacturing businesses aiming for environmentally friendly operations.
The fundamental characteristics of the factory of the future will be innovation, sustainability, digitization, and interconnection. Proactively embracing these trends can help factories remain resilient, competitive, and adaptable in a time of rapidly advancing technology and changing consumer tastes.