1. Introduction
In many different industries, equipment failure can be expensive and disruptive to operations. Equipment failure can have a negative influence on hospitals and manufacturing facilities alike by causing downtime, production delays, safety risks, and eventually financial losses. Thus, in order to prevent unplanned malfunctions and guarantee the dependability and effectiveness of equipment, preventative and predictive maintenance techniques must be put into practice. Businesses may maintain ideal performance levels and dramatically decrease downtime by being proactive and resolving any issues before they worsen.
2. Understanding Equipment Failure
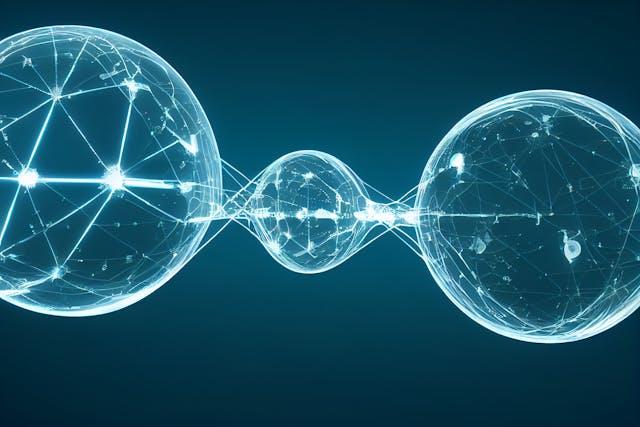
Understanding equipment failure is critical for firms to maintain operational efficiency and prevent costly downtime. Inadequate maintenance, normal wear and tear from use, unfavorable operating conditions, and manufacture flaws are common reasons for equipment failure. Equipment failure can cause production schedule disruptions, lowered product quality, worker safety issues, and higher repair or replacement expenses.
Unplanned downtime is a major effect of equipment failure. This unplanned halt to business activities may cause financial losses for the company as well as missed deadlines, unhappy clients, and lost productivity. When machinery malfunctions and there is a chance of accidents or injuries occurring at work, it can put workers in danger.
By understanding the frequent causes and consequences of equipment failure, businesses may develop preventative and predictive maintenance techniques to limit risks and assure the reliable performance of their assets. Proactively addressing possible problems before they worsen can help companies save downtime, increase equipment longevity, raise safety standards, and eventually boost overall operational effectiveness.
3. Preventive Maintenance
In order to identify possible problems before they arise, preventive maintenance is a proactive approach to equipment upkeep that entails routinely scheduled inspections, repairs, and replacements. Businesses may decrease total downtime, increase equipment longevity, boost worker safety, and improve reliability by following a preventive maintenance program.
Preventive maintenance has many advantages. First and foremost, by spotting and fixing little errors before they worsen, it helps prevent unplanned malfunctions. This guarantees that production schedules are not thrown off by equipment breakdowns and also saves time and money. Second, businesses can avoid future expensive repairs or replacements by doing routine maintenance to keep their equipment in top condition. Over time, lower operating costs can be achieved by implementing preventive maintenance to increase energy efficiency. By extending the life of equipment and boosting productivity, proactive maintenance can make a business more profitable and efficient in the long run.
4. Implementing Preventive Maintenance Strategies
In order to prevent equipment failure, a preventative maintenance program must be put in place. To create an efficient preventive maintenance plan, many approaches can be used for various kinds of equipment.
Establishing a regular maintenance and inspection schedule for manufacturing equipment according to the manufacturer's instructions is essential. Tracking performance metrics with sensors and monitoring systems can also assist in seeing possible problems before they become expensive malfunctions.
When it comes to fleet cars, having a checklist for drivers to check each day might assist identify little issues early on. Regular tire rotations, engine tune-ups depending on mileage intervals, and fluid checks are crucial procedures to keep the cars operating at their best.
System failures and data loss can be avoided when it comes to IT equipment by making sure software updates are deployed on a regular basis and performing frequent data backups. An other way to increase the lifespan of computer hardware is to set in place a schedule for cleaning circuit boards and fans.
Ensuring the dependable operation and extended lifespan of various types of equipment necessitates customizing preventive maintenance procedures to meet their unique requirements. These procedures can be added to regular maintenance plans to help firms minimize downtime, lower repair costs, and extend the life of their expensive assets.
5. Predictive Maintenance Techniques
Predictive maintenance strategies employ cutting-edge technology such as the Internet of Things (IoT) and Artificial Intelligence (AI) to foresee probable equipment faults before they occur. Real-time data on a variety of characteristics, including as vibration, pressure, and temperature, can be continuously collected and evaluated by utilizing IoT sensors integrated into machinery. After that, this data is evaluated by AI algorithms that are able to identify trends that could point to a potential issue.
Beyond routine inspections, predictive maintenance offers a proactive strategy that helps companies avoid expensive downtime and unplanned malfunctions by resolving problems before they become more serious. Long-term maintenance expenses are decreased in addition to improving operational efficiency through the inclusion of predictive maintenance technologies. Businesses can move from a reactive maintenance paradigm to a more strategic, data-driven strategy that optimizes equipment uptime and productivity by implementing predictive maintenance techniques.
6. Benefits of Predictive Maintenance
Reducing downtime and improving equipment reliability are two major advantages of predictive maintenance. Equipment can be kept under constant observation by using sensors and data analysis to spot any problems before they become serious malfunctions. This proactive strategy reduces downtime and prevents unplanned breakdowns by enabling prompt maintenance actions. Predictive maintenance extends the life of machinery and eliminates needless repairs, which lowers costs by optimizing maintenance schedules. The implementation of this method results in increased production and overall operational efficiency as equipment is available when needed most.
7. Combining Preventive and Predictive Approaches
Equipment maintenance can be made even more efficient by combining predictive and preventative maintenance techniques. Organizations can establish a comprehensive maintenance program that guarantees operating efficiency, minimizes downtime, and lowers costs by utilizing the strengths of both techniques.
Combining conventional preventive maintenance plans with predictive maintenance methods such as vibration analysis, infrared thermography, and oil analysis is one useful suggestion. It is possible to proactively identify potential faults before they develop into expensive failures by including real-time data collecting and analysis into routine preventive maintenance procedures.
Creating open lines of communication between the maintenance teams in charge of the various maintenance tasks is another sensible strategy. Working together, predictive maintenance experts and preventive maintenance personnel may better coordinate efforts, share information, and align plans for optimal effect.
Investing in training programs that equip maintenance professionals with the knowledge to comprehend and exploit both preventive and predictive maintenance procedures is vital. Organizations can maximize the performance and dependability of their equipment over time by cultivating a culture of knowledge exchange and continual development within the maintenance team.
Organizations may increase asset dependability, prolong equipment lifespan, and promote overall operational success by fusing predictive and preventive maintenance techniques into a coherent strategy that is customized to the unique requirements of their operations and equipment.
8. Case Studies
When it comes to maintenance techniques, case studies are a great way to grasp the true effects of predictive and preventative maintenance methods. Let's examine a few striking instances when these tactics have been successful in minimizing operating inefficiencies and preventing equipment failure.
Case Study 1: Manufacturing Industry
Predictive maintenance methods were implemented, and they completely changed the way a huge manufacturing unit operated. The maintenance staff was able to obtain up-to-date information on the state of the equipment by installing condition monitoring sensors on crucial machinery. By taking a proactive stance, they were able to identify wear and tear early on and make targeted changes before severe breakdowns happened. Consequently, there was a notable reduction in downtime, an enhancement in production efficiency, and a 20% decrease in overall maintenance expenses.
Case Study 2: Aviation Sector
One of the industry's top airlines established preventative maintenance plans according to flight duration and component life estimates. By means of rigorous monitoring of every aircraft's performance parameters and the examination of past data, they were able to plan maintenance operations like engine overhauls and part replacements in a timely manner. By preventing unanticipated malfunctions during flights, this foresight maximized aircraft availability and guaranteed passenger safety. The airline recorded a significant rise in fleet dependability along with a 15% decrease in unplanned maintenance incidents.
Case Study 3: Healthcare Facilities
Predictive maintenance software is used by hospitals to maintain their medical equipment in settings where continuous operation is essential. They prevented problems like worn-out parts or calibration errors by using IoT technology to monitor essential equipment like ventilators and MRI scanners. If the biomedical engineering team had automatic notifications for approaching faults, they could respond quickly to issues without compromising patient care. By simplifying maintenance tasks, this proactive approach not only increased staff productivity but also increased the lifespan of the equipment.📜
The aforementioned case studies highlight the concrete advantages that firms can obtain by using predictive and preventive maintenance approaches. Businesses in a variety of industries can strengthen their infrastructure against expensive downtime and unplanned failures by making investments in technology-driven solutions and cultivating a proactive asset management culture. Implementing insights acquired from these success stories can empower firms to keep ahead of equipment concerns and generate sustainable operational excellence.
9. Maintaining Compliance Standards
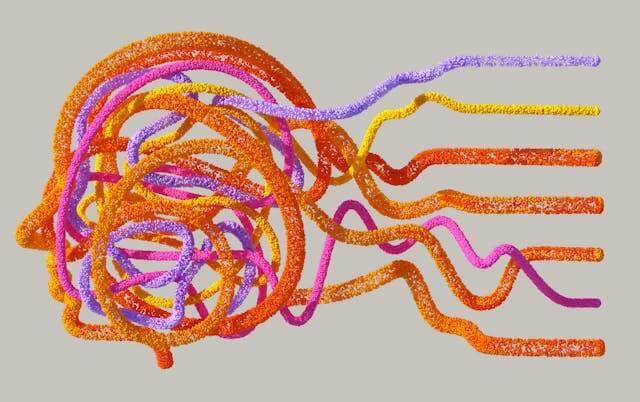
It's critical to uphold compliance standards when it comes to equipment maintenance. Following industry guidelines guarantees that the machinery is operating securely and effectively, lowering the possibility of mishaps or malfunctions. Businesses can show their dedication to quality and safety by adhering to the routine maintenance procedures outlined by applicable standards. This will build trust with both regulatory bodies and customers. In addition to endangering the equipment, noncompliance with these requirements may have negative legal and financial repercussions for the company. In order to prevent equipment failure and guarantee efficient operations, any firm should place a high premium on adhering to compliance regulations.
10. Tools and Software for Maintenance Management
Using tools and software can greatly expedite preventative and predictive maintenance efforts in the field of maintenance management, assuring equipment reliability and reducing unplanned breakdowns. Many software programs, such as Computerized Maintenance Management Systems (CMMS), provide functions like inventory management, work order tracking, scheduling maintenance tasks, and report generation to help with decision-making.
Certain tools, such vibration analysis equipment, thermography cameras, and oil analysis kits, are specifically made for condition monitoring. With the use of these technologies, maintenance staff may evaluate an asset's health in real time and spot possible problems before they become expensive breakdowns. An even more all-encompassing approach to asset management is made possible by combining these instruments with predictive maintenance software.
The development of smart sensors and devices that can remotely gather data on machine performance and condition has been made possible by advancements in Internet of Things (IoT) technology. Proactive maintenance plans that target specific components based on actual usage and wear patterns are made possible by the processing of this real-time data by specialist software, which offers insights into equipment health and performance trends.
Organizations can go from reactive to proactive maintenance procedures by utilizing the capabilities of contemporary tools and software for maintenance management. This change improves operational productivity and efficiency overall while also extending the life of important assets. Leveraging these cutting-edge technologies will be essential to successfully preventing equipment failure and long-term maintenance process optimization as technology advances.
11. Training and Skill Development
Developing one's skills and receiving training are essential for successfully executing maintenance measures. Technicians are essential to maintaining equipment functionality and lowering the likelihood of malfunctions. Organizations may give their technicians the skills and knowledge they need to perform predictive and preventative maintenance jobs effectively by providing them with sufficient training.
Investing in technician training programs can result in improved comprehension of how equipment operates, early identification of any problems, and appropriate maintenance procedures. In the long term, well-trained technicians can help organizations save time and money by spotting issues before they become expensive breakdowns. Additionally, ongoing training keeps personnel abreast of developments in the field, technological breakthroughs, and best practices for maintenance.
Skilled technicians contribute to increased equipment reliability, prolonged asset lifespan, and improved overall operational efficiency. Their capacity to carry out exhaustive examinations, precise diagnosis, and prompt repairs can greatly save downtime and increase efficiency. With the right training, technicians can adopt a proactive maintenance strategy that enables them to see problems before they arise and take appropriate preventive action.
To put it succinctly, the effective application of predictive and preventive maintenance procedures depends on technicians' training and skill development being given top priority. In addition to fostering a culture of continuous improvement, organizations that engage in their workers by offering ongoing training opportunities also guarantee the optimal performance of their equipment systems. By empowering technicians with the necessary knowledge and skills, firms may avoid risks associated with equipment failure and achieve sustainable operational excellence.
12. Conclusion
Preventing equipment failure is mostly dependent on proactive maintenance measures. Businesses may lower downtime, save repair costs, and improve operational efficiency by putting preventative and predictive maintenance strategies into practice. Organizations may ensure seamless operations and extend the lifespan of equipment by addressing issues before they become failures through regular inspections, prompt replacements, and predictive analytics. Stressing the value of preventive maintenance protects investments and improves overall output and customer satisfaction. Keep in mind that spending money on maintenance now will pay off in the long-term dependability and durability of your machinery.