1. Introduction
For machinery and equipment in a variety of industries to operate smoothly, maintenance procedures are essential. Many firms are using cutting-edge technology like Artificial Intelligence (AI), Internet of Things (IoT), and Computerized Maintenance Management Systems (CMMS) to improve and streamline maintenance processes.
A computerized maintenance management system (CMMS) is a software program that assists companies in efficiently managing their maintenance operations. It helps with work order tracking, task scheduling, inventory management for spare parts, and historical data analysis for optimal maintenance plans. Predictive maintenance based on patterns in equipment performance is made possible by IoT technology, which connects devices and allows them to exchange real-time data and communicate with one another. Massive data sets can be analyzed by AI algorithms to find trends, anticipate possible faults, and recommend the best maintenance plans.
Proactive maintenance is essential to limiting downtime, cutting costs, and optimizing operating efficiency in today's fast-paced industrial environment. Along with increasing asset reliability, the integration of CMMS, IoT, and AI in maintenance operations gives businesses the flexibility to make data-driven decisions that provide them a competitive edge in their respective markets.
2. Understanding CMMS
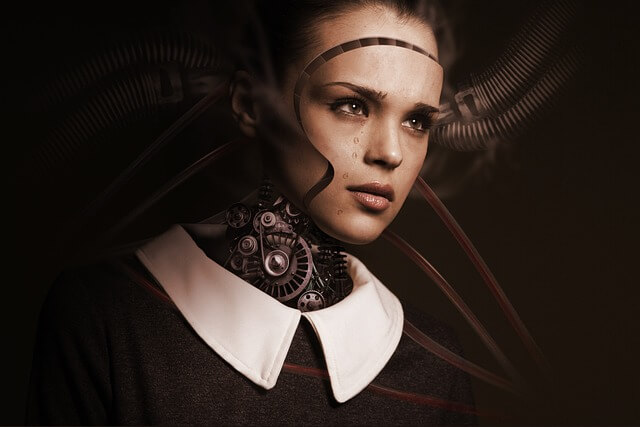
The term "CMMS," which stands for "Computerized Maintenance Management System," refers to a software program that makes asset management and maintenance chores more efficient in maintenance operations. It supports work order tracking, maintenance task scheduling, inventory management, and data collection for equipment performance optimization within businesses. Users may easily access vital asset information, including manuals, warranties, and repair histories, by centralizing the storage of such data in a CMMS system.
Preventive maintenance scheduling, which lowers downtime by proactively maintaining equipment before breakdowns arise, is one of the key purposes of CMMS. It also helps with work order monitoring and labor hour tracking for maintenance chores, which increases productivity and efficiency. By automating reordering procedures in accordance with usage trends and planned repair requirements, CMMS aids in the management of spare parts inventories.
The benefits of CMMS implementation in maintenance operations are numerous. Enhanced asset uptime via proactive maintenance scheduling based on real-time data analysis is one of the main benefits. As a result, there is less downtime and money spent on unplanned repairs or breakdowns. By streamlining labor hours and inventory control, CMMS improves resource allocation and eventually boosts operational efficiency.
Through reporting and analytics functions, CMMS offers useful insights that assist organizations in making defensible judgments about asset performance and maintenance plans. Organizations can enhance their maintenance operations' regulatory compliance adherence and overall responsibility by centralizing asset information and historical data within the system.
3. Leveraging IoT in Maintenance
In the context of maintenance, the Internet of Things (IoT) is a network of linked devices that gather and share data in order to streamline maintenance procedures. Due to the sensors incorporated in them, these Internet of Things devices can track a number of characteristics in real time, including pressure, temperature, and performance data. Maintenance staff may make better decisions by remotely monitoring the performance, condition, and consumption patterns of equipment by utilizing IoT technologies.
The ability to monitor assets in real time during maintenance operations is made possible in large part by IoT devices. These devices give maintenance crews real-time information on the functioning and health of the equipment through continuous data gathering and transmission. Proactive monitoring enables firms to swiftly address maintenance needs before they become costly failures by enabling the early detection of potential issues or abnormalities.
Through the use of machine learning algorithms and advanced analytics, IoT devices play a key role in allowing predictive maintenance methods. Predictive maintenance systems are capable of predicting the likelihood of equipment failure and recommending the best maintenance plans by evaluating the massive amounts of real-time data produced by IoT sensors. By extending asset lifespans and decreasing downtime, proactive maintenance replaces reactive maintenance, improving overall cost-effectiveness and operational efficiency for businesses.
4. The Impact of AI on Maintenance Operations
By transforming established procedures, artificial intelligence (AI) significantly improves maintenance operations. AI is making maintenance procedures more efficient and predictive than they have ever been. Predictive analytics is a major use of AI in maintenance, where algorithms evaluate past data to precisely anticipate future equipment faults. Businesses can schedule maintenance work proactively, limiting downtime and drastically lowering operating costs, by anticipating problems before they arise.
Another potent AI technique that is revolutionizing maintenance operations is machine learning. Organizations can obtain important insights from data generated by sensors and Internet of Things (IoT) devices installed on machinery by utilizing machine learning algorithms. These observations enhance asset performance, optimize maintenance schedules, and eventually increase equipment lifespan. Machine learning gives systems the ability to learn from the past and make decisions in maintenance tasks better over time.
AI integration in maintenance operations opens the door for autonomous systems that can carry out activities with little assistance from humans. These self-sufficient systems possess the ability to autonomously diagnose problems, plan fixes, and even carry out regular maintenance tasks. Organizations may boost productivity, optimize maintenance procedures, and free up human resources for more important jobs requiring critical thinking and problem-solving abilities by using AI technologies to automate these repetitive operations.
Artificial intelligence is completely reinventing the field of maintenance operations, not only altering its environment. Artificial Intelligence (AI) is enabling businesses to manage their assets proactively, optimize performance, and achieve operational excellence like never before. This includes predictive analytics, machine learning, and autonomous systems. AI will surely save money in the long run by reducing downtime, increasing productivity, and improving overall equipment efficacy. For this reason, it will play a crucial role in maintenance management going forward.
5. Integration of CMMS, IoT, and AI
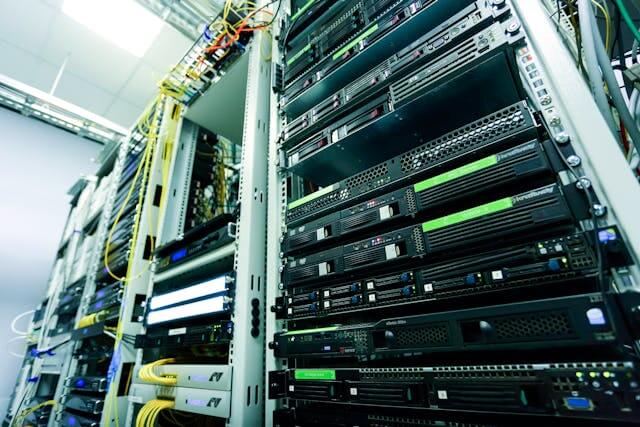
There are many benefits to integrating CMMS, IoT, and AI for a comprehensive maintenance strategy. Through the integration of these technologies, establishments can attain predictive maintenance competencies, which provide proactive monitoring of equipment and prompt actions to avert malfunctions. A unified system for monitoring work orders and assets is offered by CMMS, whereas IoT sensors gather data on equipment performance in real time. This data is analyzed by AI systems to precisely forecast maintenance requirements.
Manufacturing is one industry where good integration is demonstrated. A system was established by the company in which IoT sensors monitor machine status, CMMS records equipment history and scheduling, and AI analyzes the data to forecast breakdowns. This integration led to a 20% reduction in downtime and a considerable decrease in maintenance expenses.
In a another instance, a facility management business combined CMMS with AI-powered analytics and IoT-enabled smart building solutions. They were able to save operating expenses and enhance energy efficiency by optimizing maintenance plans based on real-time usage patterns thanks to this integration. These illustrations show how CMMS, IoT, and AI integration can revolutionize contemporary maintenance operations.
6. Challenges and Considerations
When CMMS, IoT, and AI are implemented in maintenance operations, difficulties frequently occur. Integrating these technologies with current systems and procedures is a common difficulty. Ensuring compatibility and smooth data flow can be difficult and time-consuming. A further obstacle is that staff members must receive sufficient training in order to operate these new instruments. Successful implementation may also be hampered by employees' resistance to change if they are used to using traditional ways.
To optimize the advantages of CMMS, IoT, and AI, organizations looking to integrate these technologies into maintenance operations need to take into account a number of important considerations. First and foremost, it's critical to match organizational goals and objectives with technology adoption. It's crucial to comprehend how these tools can save expenses, increase production, and decrease downtime for a successful adoption. It's critical to choose the appropriate technology partners and solutions to match the unique requirements of the company. Prospective setbacks can be avoided by doing extensive study and due diligence prior to committing to a specific platform or service.
Data security and privacy must be given top priority by organizations when CMMS, IoT, and AI are integrated into maintenance operations. It is crucial to have strong cybersecurity safeguards in place to safeguard private data and stop illegal access. To make sure that data protection procedures continue to be effective against new risks, regular audits and modifications should be carried out. Lastly, encouraging an innovative and continuous improvement culture inside the company is essential to ensuring that these cutting-edge technologies are successfully used in maintenance operations. Fostering an atmosphere that is conducive to technical progress can involve promoting experimentation, drawing lessons from mistakes, and acknowledging achievements.
7. Future Trends
The ongoing convergence of CMMS, IoT, and AI technologies is poised to change maintenance operations in the future. New developments point to a move in the direction of predictive maintenance, driven by real-time data analytics from Internet of Things sensors and devices. Maintenance teams can now adopt proactive rather than reactive tactics, which will save expenses and downtime.
Anticipate a rise in automation in maintenance duties in the upcoming years thanks to AI-driven algorithms that can detect equipment breakdowns, optimize schedules, and streamline processes. Because of this automation, maintenance procedures will be more productive and efficient, lowering the possibility of human error and increasing the overall effectiveness of the equipment.
The adoption of condition-based maintenance techniques, which depend on ongoing equipment health monitoring, is anticipated to be fueled by the confluence of CMMS, IoT, and AI. By using this method, companies can increase asset longevity and reliability by prioritizing maintenance work based on real asset performance data rather than established schedules.
With the help of these technologies, maintenance procedures will change from being purely reactive to being proactive and predictive. Organizations may proactively manage their assets, optimize resources, and eventually reach higher levels of operational excellence in the future by combining the capabilities of CMMS, IoT, and AI.
8. Case Studies
Case Study 1: Manufacturing Company X Manufacturing Company X implemented a CMMS system integrated with IoT sensors to monitor their production equipment. By leveraging AI algorithms, the system predicted maintenance needs accurately, preventing costly breakdowns. This proactive approach resulted in a 20% reduction in downtime and a 15% increase in overall equipment efficiency.
Case Study 2: Transportation Company Y✌️
Transportation Company Y collected real-time performance and condition data on their fleet of vehicles by using IoT devices. Through their CMMS platform, AI analyzed this data, allowing the organization to optimize maintenance plans based on predicted insights. They were able to improve fleet safety and reliability while also cutting maintenance expenditures by 25% as a result.
These case studies show how CMMS, IoT, and AI working together can transform maintenance operations in a variety of sectors. Organizations can greatly increase overall operational efficiency, expedite maintenance procedures, and extend asset lifespan by utilizing data-driven insights for proactive decision-making.
9. Best Practices for Implementation
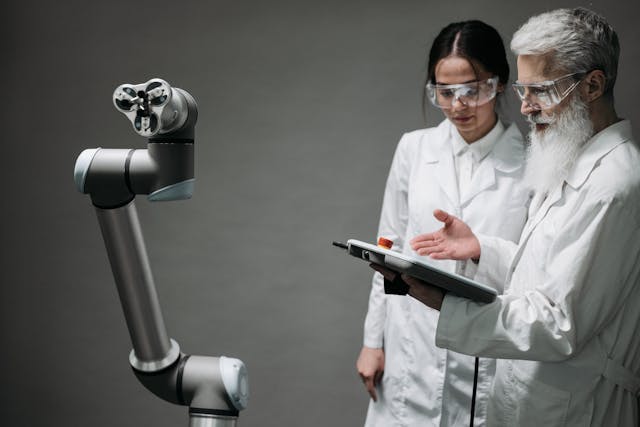
Implementing CMMS, IoT, and AI solutions in maintenance operations requires careful planning and execution. Here are some best practices to consider for a successful deployment:
1. **Establish Specific Goals:** Establish precise goals and objectives for the IoT, CMMS, and AI technology integration into your maintenance procedures. Determine the most important places where these solutions can be most helpful.
2. **Cross-functional Team Collaboration:** In order to guarantee objective alignment and smooth departmental integration, include stakeholders from maintenance, IT, operations, and management in the implementation process.🤝
3. **Data Quality and Integration:** Make sure that data flows between CMMS, IoT devices, sensors, and AI platforms smoothly by integrating systems in a seamless manner. Reliable and consistent data is essential for making wise decisions.
4. **Training and Change Management:** Educate staff members thoroughly on how to use the new technology. Employ change management techniques to assist staff members in adjusting to the changes these solutions bring about.
5. **Increase Gradually, Start Small** To evaluate the technology's efficacy before expanding its use throughout the entire company, start with pilot programs or small-scale installations. This method facilitates the early detection of possible problems and permits modifications as necessary.
6. **Ongoing Observation and Assessment:** Make sure that CMMS, IoT devices, and AI algorithms are accomplishing the goals by routinely monitoring performance metrics and KPIs related to these technologies. Make wise judgments based on this data to ensure ongoing improvement.
7. **Technical Security Steps:** Put strong cybersecurity safeguards in place to safeguard private maintenance data that is sent between systems. Maintain adherence to industry norms and laws to protect the information assets of your company.
8. **Selection of Vendors:** Select reliable suppliers of CMMS, IoT, and AI solutions for maintenance operations who have a track record of success. When choosing a vendor, take into account aspects like future-proofing capabilities, scalability, support services, and dependability.
Organizations can optimize maintenance strategies and improve efficiency, reduce downtime, and boost overall productivity within their facilities by closely adhering to these best practices when implementing CMMS, IoT, and AI technologies in maintenance operations.
10. Cost-Benefit Analysis
When thinking about using CMMS, IoT, and AI in maintenance operations, a cost-benefit analysis is essential. Adopting these technologies comes with initial expenditures, but you should balance those against the long-term benefits they can provide to your maintenance procedures. It may appear expensive to adopt CMMS, IoT devices, and AI systems at first, but it's important to know how these technologies may enhance productivity, cut down on downtime, avoid expensive breakdowns, and streamline operations over time.
Think about things like software license fees, hardware costs for IoT sensors or devices, employee training costs for proficient use of these systems, and any required infrastructure changes when assessing the costs related to CMMS, IoT, and AI integration. Conversely, there are advantages such as the ability to perform predictive maintenance, made possible by IoT data analytics and AI algorithms, which can assist in identifying problems before they result in equipment failure.
Organizations may make well-informed decisions about integrating CMMS, IoT solutions, and AI technologies into their maintenance operations by performing a thorough cost-benefit analysis. This assessment procedure makes sure that the investment is in line with the organization's long-term cost-saving and operational efficiency objectives. By demonstrating the benefits these technologies can have on overall maintenance performance and ROI, it also aids in the justification of the expense.
11. Training and Skill Development
For maintenance operations to efficiently utilize CMMS, IoT devices, and AI tools, training and skill development are essential. Giving staff members thorough training enables them to fully utilize these technologies, improving maintenance jobs' accuracy and efficiency. Organizations may guarantee that their workforce has the capabilities needed to optimize maintenance operations by investing in training programs designed specifically for using CMMS, IoT, and AI technologies.
Employees may expedite work order management, asset tracking, and preventative maintenance scheduling by learning how to use CMMS systems. Knowing how IoT devices work gives staff members the tools they need to gather data in real time from linked assets for preventative maintenance. Workers' ability to predict equipment faults and allocate resources more efficiently can be improved by acquainting themselves with AI technologies like predictive analytics.
Ongoing training fosters an innovative culture in the maintenance department while also improving worker skill in using new technologies. Organizations may drive operational excellence and maintain their competitive edge in the continually changing field of maintenance operations by staying up to date with advances in CMMS, IoT, and AI capabilities through continuing training programs. Making training and skill development a top priority demonstrates an organization's dedication to leveraging cutting-edge technologies for improved performance and efficiency while maintaining competitiveness.
12. Conclusion
Taking into account everything mentioned above, we can say that the CMMS, IoT, and AI integration has transformed maintenance operations by improving asset performance, automating procedures, and facilitating predictive maintenance. A consolidated platform for effectively managing maintenance tasks is provided by CMMS. IoT devices make it possible to collect data from equipment in real-time to track performance and identify problems early on. Large-scale data is analyzed by AI systems to forecast equipment breakdowns and improve maintenance plans.
The industry will undergo more transformation as these technologies continue to improve and integrate. Improved predictive skills allow maintenance operations to move from reactive to proactive approaches, which lowers expenses and downtime. The maintenance industry is expected to see increases in productivity, efficiency, and safety as a result of the convergence of CMMS, IoT, and AI. In the future maintenance landscape, adopting these technologies will be essential for businesses looking to maintain their competitiveness and satisfy changing client demands.